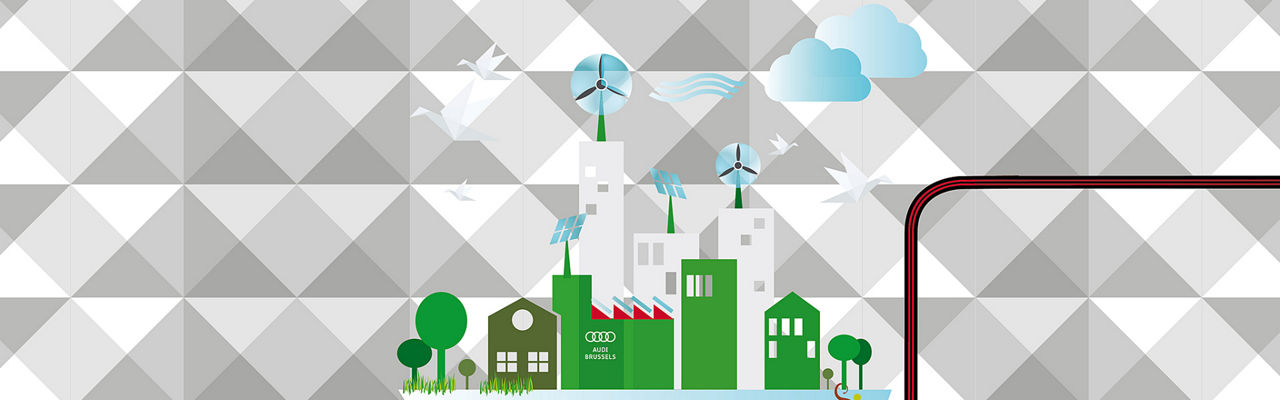
Mission:Zero
How is Audi making carbon-neutral production a reality?
Vehicle manufacturing produces CO₂ emissions at various stages, including the provision of electricity, heating or transportation at the plant.
In 2014, Audi was the first premium carmaker to determine its corporate carbon footprint according to an internationally accepted standard. It marked a key step toward transparency in the company’s greenhouse gas emissions. Today, these emissions can be analyzed in even greater detail and effectively reduced.
Brussels is an example: Production at the site is completely carbon neutral, as certified by independent experts. That makes the facility both a pioneer and a role model. It is also logical that the first purely electric series-production vehicle, the Audi e-tron, is manufactured here. This is one effort not only to secure the company’s own future, but also to play its part in achieving the strategic goal of sustainability.
Green electricity
As early as 2012, Audi in Brussels began purchasing green electricity and preventing the emission of up to 17,000 metric tons of CO₂ per year. In 2013, the largest photovoltaic system in the region was installed. In 2017 the facility was expanded. Now measuring 89,000 square meters – approximately the size of 12.5 soccer fields – it produces enough green electricity to power the equivalent of over 1.500 four-person households for one year. At the same time, heating of the plant is carbon neutral thanks to the purchase of biogas certificates. All other emissions produced by fuels, heating oil or incinerating solvents are offset through so-called carbon credit projects.
Apart from reducing CO₂ emissions, other steps are taken to improve the site’s environmental footprint. Additional projects protect the environment by conserving water and energy or reducing emissions of pollutants into the air and water.
All processes are founded on efficiency. And that includes avoiding materials that are harmful to the environment and making optimum use of resources. Cutting-edge technology is used to accomplish this.
Environmental protection in Brussels
The overview shows how diverse and extensive environmental protection is at the Brussels plant and outlines the projects underway in the production facilities.
Audi Group production sites
The following overview shows a few examples among many. They are instrumental in ensuring that the company meets its ecological targets.